Optimering af portstørrelsen og placering i en sprøjtestøbeform til en lotionpumpe gennem formflowanalyse involverer en systematisk proces med simulering, analyse og designjusteringer. Her er en trin-for-trin guide til at opnå denne optimering:
1. Definer projektmål og -kriterier:
- Start med klart at definere målene og kriterierne for sprøjtestøbeformen til lotionpumpen. Overvej faktorer som delekvalitet, cyklustid, materialeforbrug og omkostningsbegrænsninger.
2. Indsaml materialedata:
- Få nøjagtige materialedata for den specifikke plastharpiks, der skal bruges i sprøjtestøbningsprocessen. Dette inkluderer smelteflowindeks (MFI), viskositet, termiske egenskaber og andre materialeegenskaber.
3. Modeloprettelse:
- Opret en detaljeret 3D-model af lotionpumpedelen og sprøjtestøbeformen, inklusive hulrum, kerne, kølekanaler og løbesystem. Sørg for, at modellen nøjagtigt repræsenterer de påtænkte produktionsforhold.
4. Simuleringsopsætning:
- Brug software til analyse af formflow til at opsætte simuleringen. Definer sprøjtestøbningsprocesparametrene, såsom sprøjtetryk, temperaturprofiler og kølehastigheder. Angiv portplaceringerne og indledende portstørrelser.
5. Indledende simuleringskørsel:
- Kør den indledende simulering af formflow med de valgte portplaceringer og størrelser. Analyser resultaterne, herunder påfyldningstid, trykfordeling, svejseledninger og luftfældeplaceringer. Identificer eventuelle potentielle problemer eller områder til forbedring.
6. Gateplaceringsanalyse:
- Vurder egnetheden af de valgte portplaceringer. Overvej faktorer som afbalanceret fyldning af hulrum, undgåelse af kosmetiske defekter og minimering af påvirkningen af svejselinjer. Juster portens placeringer efter behov.
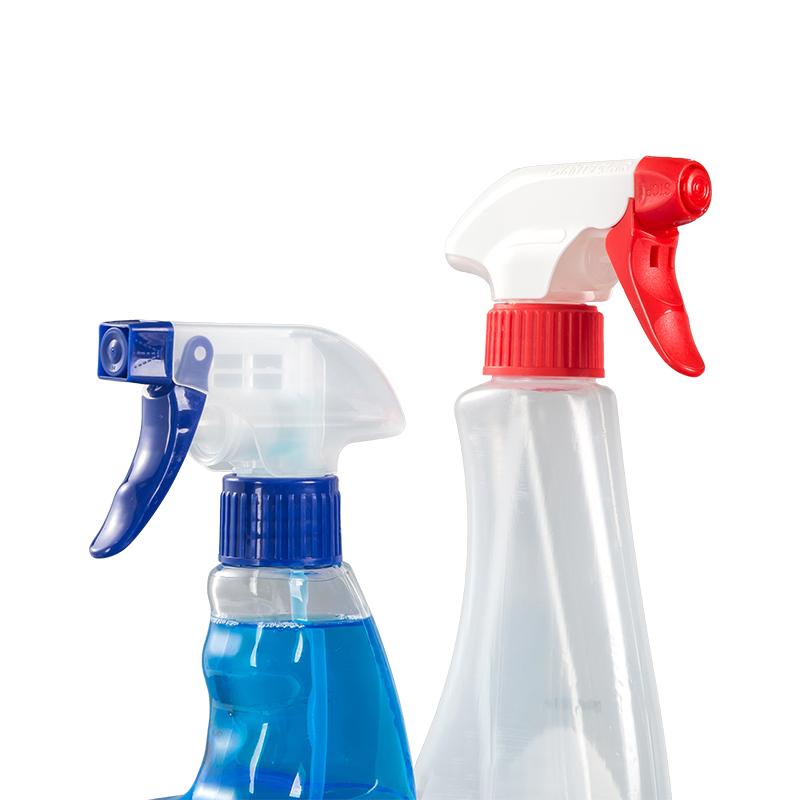
7. Portstørrelsesanalyse:
- Analyser effekten af portstørrelse på injektionsprocessen. Forøg eller mindsk gatestørrelserne gradvist i efterfølgende simuleringer for at finde den optimale størrelse, der balancerer påfyldningstid, tryk og materialeflow uden at forårsage defekter.
8. Valg af porttype:
- Afhængigt af resultaterne af portstørrelsesanalysen skal du vælge den passende porttype, såsom en indløbsport, kantport eller ventilatorport. Porttypen påvirker, hvordan materialet kommer ind i hulrummet og kan påvirke delens kvalitet.
9. Løbersystemoptimering:
- Optimer løbesystemets design for at sikre jævn materialefordeling til alle hulrum. Juster løberens dimensioner og konfigurationer for at minimere materialespild og trykfald.
10. Kølekanalanalyse:
- Vurder indvirkningen af portens placering og størrelse på køleeffektiviteten. Sørg for, at den valgte portkonfiguration ikke forstyrrer effektiviteten af kølekanalerne. Juster kølekanalens placering om nødvendigt.
11. Iterativ simulering:
- Udfør iterative simuleringer ved at foretage gradvise justeringer af portplaceringer og -størrelser baseret på analyseresultaterne. Fortsæt med at forfine designet, indtil de ønskede kriterier, såsom balanceret fyldning og minimale defekter, er opfyldt.
12. Endelig validering:
- Udfør en endelig formflowanalyse for at validere den optimerede portstørrelse og placering. Bekræft, at designet opfylder de foruddefinerede projektmål og kriterier.
13. Dokumentation og rapportering:
- Dokumenter resultaterne, inklusive den valgte portkonfiguration, simuleringsdata og eventuelle designjusteringer. Forbered en rapport, der opsummerer optimeringsprocessen og dens resultater.